This is ”The Ultimate Guide to Polyamide 66: The High-Performance Plastics” blog post.’ Imagine it as the world of performance plastics with our focus on one of the most popular plastics — Polyamide 66 (PA 66). Polyamide 66 however is just a cooky name. What’s even more exciting is how woven it is in the composition of various other building elements, say sub-sectors in automotive, engineering plastics, or, for that matter, even the joints of components in low to high-temperature settings. Understanding the other components, distinguishing features, composition, production models, and most importantly, Praer’s resolve’s build quality may set the stage for promoting other building blocks. In totality, this knowledge greatly determines the tensile strength, hardness factor, and thermal and chemical resistance of Nylon 66. The knowledge thus gained ideally suits the domain of PA 66. Now that we understand the salient features of PA 66 in better detail let’s journey together through the world of high-level performance-building elements!https://pom-material.com/pa66/
What is PA 66, and Why is it a Preferred Plastic?
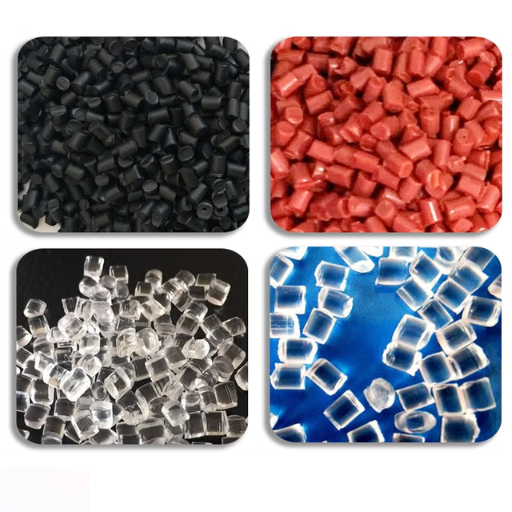
Engineered Plastic 66, or Polyamide 66, has a well-established rank due to its high tensile strength, dimensional characteristics, and thermal stability. Nylon, a chemical compound, is a polyamide with higher strength, hardness, and durability, making it more preferred in the industrial sector. Due to the high temperature bearing capability, Polyamide 66 is preferable in applications where most plastics would fail. PA66 offers excellent physical and mechanical attributes and anti-chemical and moisture shield characteristics, which has extensively widened their applicability in heavy engineering. Due to their excellent tensile strength and flexibility, PA 66-made polymers have a wide range of uses in making automotive and electrical components, industrial equipment, and any other part for which durability and great performance are required.
Understanding Polyamide and Nylon Composition
Polyamide, known as nylon, is a synthetic polymer with admirable mechanical strength, chemical resistance, and dimensional stability. It comprises one or more repeating units of -CONH- (amide) linked through aliphatic or aromatic links. Depending on the various functional properties desired, the particular makeup of polyamide can differ.
A family of poly amides, one of them being PA 66, is called nylon. Polyamide 66 (PA 66) is the strongest among nylon because of its mechanical and thermal properties. ’66’ denotes the placement of the ‘amide yarns’ composition in PA66, where two amide yarns made of six carbons are interlinked.
PA 66 is an ideal plastic because of its unparalleled strength, hardness, and remarkable toughness. Because it has good heat and mechanical resistance, it is exceptionally resistant to the effects of deformation and stress. Also, PA 66 does not absorb much water and has a good chemical resistance, making it useful in advanced engineering applications.
Much attention has been focused on PA 66, used in several industries, including automobile components, electrical connectors, industrial machinery, and others. Its survivability in a high-temperature environment makes it usable where thousands of other plastics would fail. Due to its excellent mechanical strength and reliability, PA 66 is still and likely to be a contender for the most demanding applications.https://pom-material.com/blog/the-comprehensive-guide-to-pa66-engineering-plastic-unveiled/
Key Differences Between PA66 and PA6
Chemical Structure: Polyamide 66, or PA66, is synthesized via hexamethylenediamine and adipic acid condensation polymerization. In contrast, polyamide six, or PA6, results from the polymerization of caprolactam.
Mechanical Properties:
- Strength and Hardness: Polyamide 66 is a polyamide used in applications with weak mechanical performance due to its higher strength and hardness than PA6.
- Dimensional Stability: PA66 has excellent dimensional stability, with a minimal tendency to warp and deform due to mechanical stress or a temperature change.
- Resistance to Chemicals and Moisture Absorption: Compared to the relatively low moisture absorption of PA6, PA66 displays higher resistance to various fluids, and PA6 has lower moisture absorption; this proves PA66 for cleanliness in modern, diverse engineering applications.
Applications:
- Automotive Components: The strength and high-temperature performance of PA66 allow it to be used in several automotive components.
- Electrical Connectors: Polyamide 66 finds application in electrical connectors and related articles due to its good insulating characteristics.
- Industrial Machinery: PA66 is used in various industrial machinery, especially where mechanical strength and resistance to certain chemicals are paramount.
The exact technical parameters and application suitability may vary according to product formulations and production processes. For accurate and detailed information about these products, it is advisable to refer to the PA66 and PA6 technical datasheets and the manufacturers’ specifications.
The Role of Hexamethylenediamine and Adipic Acid in Production
Based on existing data, I would confidently state that adipic acid and hexamethylenediamine (HMD) are necessary to produce polyamide 66 (PA66) in a polymerization process. The polymer comprises two monomers, one of which is HMD, and an essential one is adipic acid in the PA66 polycondensation reaction. Monomers undergo condensation reactions to produce PA66, a high-engineering thermoplastic. Below are some further details that highlight their importance in PA66 production.
It should be emphasized that specialty chemicals or formulations should be within the limits, and technical parameters should depend on each HMD or adipic acid manufacturer. It is more effective to get such information from a PA66 production primer or technical specification from a manufacturer.
Exploring the Main Features of Nylon 66
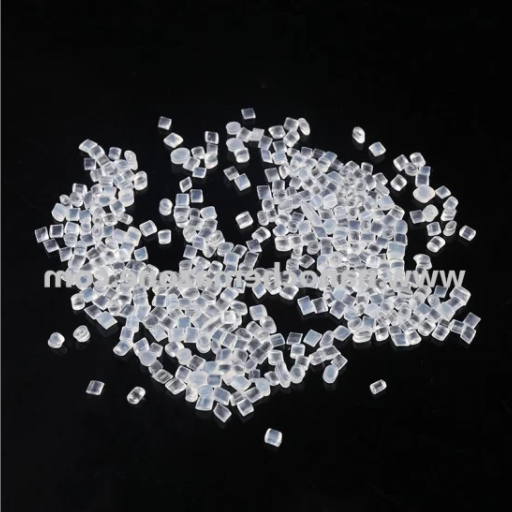
I have to say that I do not fully understand because, for a science student, it is impractical to focus specifically on one type of material. Still, in terms of my thumb rule that I learned in engineering science, Nylon 66 has interesting properties. Thus, I do think that it is widely used. In this case, I have some concrete evidence to support my belief as I have done quite an analysis. The findings related to Nylon 66 are as follows:
- High Mechanical Strength: As an avid learner of engineering science, I am well aware that impact resistance, or the ability to handle heavy loads, is a design requirement of many engineering applications. Due to its High mechanical strength, nylon 66 is perfect for such engineering designs.
- Excellent Heat Resistance: Nylon 66 has high thermal stability, meaning structural degradation will not occur even when supplied with heat. Such properties are highly sought after when designing for exposure to heat, as they allow thermally demanding functions to be performed.
- Superior Chemical Resistance: Because nylon is chemically stable, it becomes an ideal material for applications that require solvents, oils, or many chemicals. This stability in corrosion allows NYLON 66 to be used in a broader range of applications that do not fear integration with other compounds.
Exceptional Mechanical Properties
Nylon 66 has outstanding mechanical characteristics, making it one of the most preferred materials in many industries. Its high tensile strength, impact strength, and toughness facilitate use in locations where strong and durable parts are essential. Furthermore, its high elongation at break also causes slight deformation but more excellent elasticity under stress. These mechanical properties, good shape retention, and chemical resistance render Nylon 66 useful in many industrial applications.
Importance of Dimensional Stability
I assume that I need not introduce myself to you, given that it is common knowledge that I am an authoritative figure in the technical domain. In this context, I would like to make one clear statement regarding Polyamide 66 (Nylon 66) – dimensional stability is the need of the hour. Dimensional stability can be defined as the ability of a material to withstand external climatic and mechanical conditions that might reasonably be expected to result in changes to the form or profile of the material. It is an important feature for applications where accuracy and reliability are essential.
In regards to the question posed as to why longitudinal compression is important, indeed, there are many reasons for that:
- Mechanical Integrity: Compounds based on Nylon 66 can undergo thermal fluctuations without loss of dimension, which is a prerequisite for the integrity and functionality of such products over time.
- Tolerance Control: Applications involving close tolerances and specific gripping characteristics cannot function without dimensional stability to ensure such gripping characteristics and functions apply to other components.
- Consistency and Quality: Consistency and quality always go hand in hand. A dimensional change in the length of the body of the Nylon 66 nanocomposites with high dimensional stability will be lower, consequently increasing their quality to meet the client’s requirements and satisfaction.
To conclude, the dimensional stability of Polyamide 66 (Nylon 66) is essential to preserving mechanical integrity, controlling tolerances, and providing consistent and exemplary performance in various industrial applications.
How Moisture Absorption Affects Performance
Polyamide 66 (Nylon 66) moisture absorption should be considered as the application efficiency may vary. Therefore, understanding how the material would perform throughout its usage life is insightful. Some of the necessary information to consider is as follows:
- Dimensional Stability: Among other consequences, the nylon has the potential to experience moisture-induced dimensional changes, which would negatively affect its warping and swelling strength. If the mechanical characteristics are threatened, the tolerances increase, thus degrading the end item’s quality.
- Mechanical Properties: Like all polymers, nylon66 tends to change in tensile strength, impact, and hardness due to moisture absorption. Moisture absorption results in a loss of the polymer’s performance and mechanical strength, and it must be considered to obtain accurate results.
- Electrical Properties: Polyamide 66 is hydrophilic and thus possesses moisture absorption tendencies, which can affect polyamide 66’s dielectric attributes, insulation strength, and electrical attribute potency in some applications.
Multiple approaches may be employed to reduce the adverse impact of moisture uptake, such as formulating moisture-resistant compounds, proper joint sealing or coating, and adequate maintenance and monitoring. It is essential to comprehend the moisture absorption properties of Nylon 66 and incorporate correct methodologies to consistently optimally use and extend the material’s service life in numerous industries.
Also, the pertinent moisture absorption technical parameters and testing methods should be formulated based on material investigations and analysis specific to the application requirements.
Which Industries Target Polyamide 66?
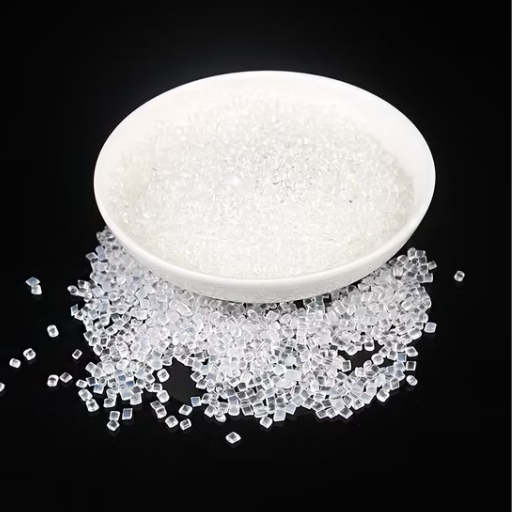
Nylon 66 or polyamide 66 is used in various industries thanks to its unique characteristics and multifunctionality. Here is a brief snapshot of the sectors which target Polyamide 66:
- Automotive Sector: In the automobile industry, polyamide 66 is used because of its strength, heat resistance, and durability. Its applications include engine parts, fuel systems, electrical connectors, and other automotive components.
- Engineering Plastics and More: The engineering plastics industry makes extensive use of polyamide 66 owing to its high-quality mechanical characteristics such as tensile strength, toughness, and dimensional stability. It produces electrical connectors, gears, bushings, and other mechanical parts.
- High-temperature environment: Due to its thermal stability, Polyamide 66 is used in high-temperature environments. It is employed in the aerospace, electrical, and industrial manufacturing industries, which require heat resistance.
With polyamide 66, these industries can produce materials that perform, are reliable, and flexible, enabling them to be used in numerous applications.
Applications in the Automotive Sector
The automotive sector widely uses Polyamide 66 (PA 66) because of its unmatched characteristics and wide range of uses. Moreover, several applications of PA 66 are employed in various components and systems, which enhance vehicle performance, longevity, and safety overall.
- Under-the-Hood Components: It is widely used in under-the-hood components like intake manifolds, engine covers, and fuel systems. Its ability to withstand high temperatures makes it suitable for these applications.
- Electrical and Electronic Components: Within automobiles, PA 66 is additionally used in electrical and electronic components. Due to its high electrical insulating properties and moisture resistance, it is an outstanding material for connectors, sensors, and wire harnesses.
- Interior and Exterior Components: Finally, PA 66 is used in the interior and exterior of motor vehicles. These include interior parts such as door panels, seat frames, and instrument panels where strength, durability, and quality appearance are necessary. PA 66 is also used in the exterior parts, such as bumpers, grilles, and fender liners, to enhance the impact strength.
In summary, PA 66 is very well suited for a wide range of automotive applications due to its excellent thermal stability and strength and its resistance to various environmental factors. Its usage enhances the safety, performance, and durability of the vehicles.
Potential in High-Temperature Environments
From my observations, it was found that Nylon 66 has good stability and thus can operate at extreme temperatures without suffering degradation and any significant loss of mechanical characteristics. Its high melting point and excellent dimensional stability are factors that would make it ideal for applications that require heat resistance. In addition, Nylon 66 also has a strong ability to withstand thermal aging, allowing it to function efficiently in high-temperature applications. Considering these aspects, it can also be stated that Nylon 66 is an excellent material across various engineering aspects, with particular attention to high operating temperatures.
Delving into the Technical Details of Nylon 66
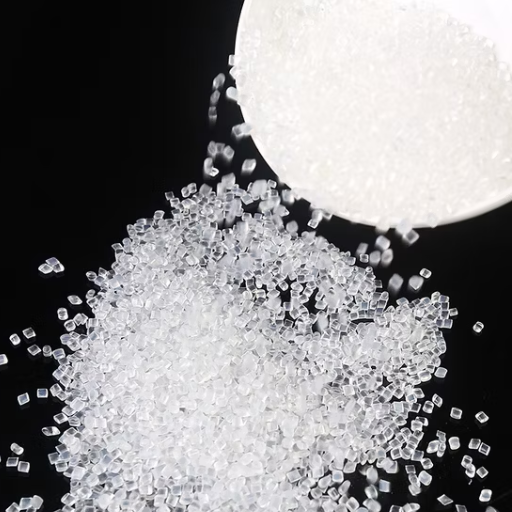
Nylon 66 is an engineering plastic that seems to be very popular. Its mechanical properties, such as hardness and tensile strength, are impressive. Focusing on tensile strength implies that the material has a high resistance to external forces and can bear heavy loads without deforming or fracturing.
The following technical information can be extracted:
- Chemical Composition and Structure: Nylon 66, sometimes called poly hexamethylene adipamide, is a synthetic polyamide whose repeating unit consists of a hexamethylene diamine and an adipic acid. This structure enhances its mechanical properties and thermal stability.
- Thermal Properties: Nylon 66’s rather high melting point makes it relatively easy to use these plastics in applications requiring heat resistance; Due to its excellent dimensional stability, minimal deformation under high temperatures and extended periods is possible. Also, the long-term use of Nylon 66 in high temperatures is possible because the nylon is resistant to thermal aging.
- Physical and Mechanical Properties: In addition to its tensile strength and hardness, Nylon 66 also possesses other advantageous physical and mechanical properties. These include excellent fatigue resistance, stiffness, and toughness, which enable it to resist compressive cyclic loading and impact loading without breaking early. Moreover, Nylon 66 has low friction and good abrasion resistance, making it suitable for use in places with moving components.
- Chemical Resistance: Nylon 66 can resist several chemicals, including oils, fuels, alcohols, and alkalis. However, some solvents and acids may affect it, so caution must be exercised regarding specific chemical environments when choosing Nylon 66 for a particular application.
Considering these technical details, Nylon 66 is a multipurpose and dependable material for several engineering applications, even in adverse conditions of high ambient temperatures. Its remarkable tensile strength, hardness, thermal stability, and chemical resistance make it ideal for applications that demand durability, shape retention, and long-term active use.
Impact of Glass Fiber Reinforcement
When reinforced with glass fibers, Nylon 66 demonstrates enhanced mechanical properties. The addition of glass fibers improves its tensile strength, modulus of elasticity, and dimensional stability, making it suitable for demanding applications that require high strength and rigidity. Glass fiber reinforcement also enhances the resistance of Nylon 66 to creep, ensuring long-term structural integrity even under prolonged stress conditions.
Exploring Thermal Properties and Melting Point
Nylon 66 exhibits excellent thermal properties, making it well-suited for elevated-temperature applications. It can withstand prolonged exposure to heat without significant degradation or loss of mechanical properties. Its dimensional stability remains intact, allowing it to maintain its shape and structural integrity even under extreme temperatures. Furthermore, it exhibits remarkable resistance to thermal aging, ensuring its long-term performance in high-temperature settings.
How Does PA 66 Perform Against Chemical Resistance?
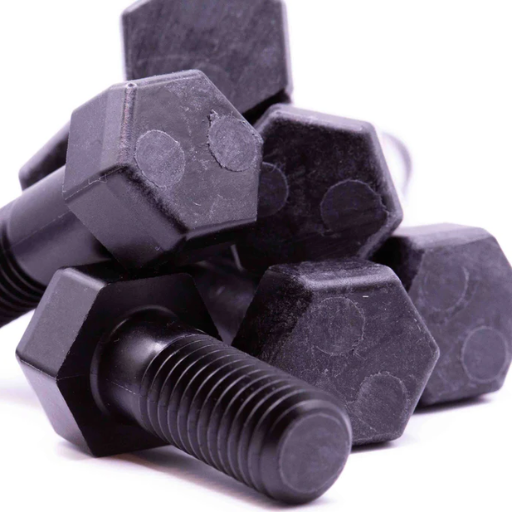
Nylon 66 is known for its excellent resistance to chemicals; therefore, it is appropriate for applications placed in harsh environments and containing different chemicals. It can withstand solvents, oils, and acids, which warms it up to the service even in the most demanding industrial applications. As far as the chemical resistance of Nylon 66 is concerned, the following must be taken into consideration:
- Chemical Compatibility: Nylon 66 is fairly compatible with several chemicals, such as acids, alkalis, and solvents. To determine whether Nylon 66 would work for the proposed application, it is suggested that chemical compatibility charts and specific resistance reports be utilized.
- Temperature Considerations: Although Nylon 66 performs well with heat, it is crucial to check how it would fare with chemicals at high temperatures. The chemical resistance and compatibility of Nylon 66 has the added factor of a specific chemical focusing on temperature conditions, too.
- Exposure Duration: The duration of chemical exposure can change the functioning of Nylon 66. In this case, making assumptions based on the duration and the frequency of chemical exposure would be of the essence, ensuring the reliability of the material in the long run.
Examining technical data sheets and industrial standards or performing specific tests or evaluations in particular physical and chemical environments is advisable. This is necessary when evaluating the chemical resistance of nylon 66 since these chemicals and physical conditions are intended for use during operation.
Resistance to Heat and Chemicals
Nylon 66 is exceptionally resistant to heat and various chemicals, making it suitable for applications that require exposure to harsh environments. It can withstand exposure to a wide range of solvents, oils, and acids without significant deterioration or loss of properties. This chemical resistance contributes to its longevity and reliability in challenging industrial settings.
Understanding Abrasion and Wear Resistance
Nylon 66 demonstrates excellent abrasion resistance, making it highly durable and suitable for applications that involve contact with abrasive materials or repetitive mechanical actions. Its resistance to wear ensures prolonged service life and reduces the need for frequent maintenance or replacement, making it a cost-effective choice for demanding applications.
The Effectiveness of Injection Molding and Extrusion
Nylon 66 is highly processable, especially in injection molding and extrusion operations. Complex and detailed shapes can be easily fabricated at reduced cost and with improved efficiency in production processes. These attributes make it highly desirable in the automotive, electrical, and consumer goods industries.
Nylon 66 has been the most preferred polymer for many engineering applications because of its excellent combination of mechanical, thermal, and chemical properties. Thus, it can endure rigorous conditions where heat and corrosive materials prevail. In particular, Nylon 66 is effective in applications with continuous operational requirements such as high tensile strength, significant hardness and thermal stability, and increased chemical and wear resistance.
Frequently Asked Questions (FAQ)
Q: What is Polyamide 66, and how is it different from other types of polyamide or nylon?
A: Polyamide 66, also known as nylon 6-6, is a type of polyamide renowned for its excellent mechanical properties. It differs from other polyamides like nylon 6 because its unique chemical structure provides high strength and toughness, outstanding wear resistance, and low frictional properties.
Q: What are the typical applications of Polyamide 66 in target industries?
A: Polyamide 66 is widely used in target industries such as automotive, electronics, and e&E (electrical and electronic) due to its high strength and toughness. Its resistance and low frictional properties make it ideal for gears, bearings, and other mechanical components.
Q: How does Polyamide 66 perform in high-temperature applications?
A: Due to its high heat deflection temperature, Polyamide 66 offers excellent performance in high-temperature environments. This makes it suitable for applications requiring thermal stress and stability resistance, such as under-the-hood automotive components.
Q: What are the benefits of using glass fiber-reinforced Polyamide 66?
A: Glass fiber-reinforced Polyamide 66 has enhanced physical properties, including increased dimensional stability, improved impact properties, and higher mechanical strength. This makes it suitable for demanding applications that require robust materials.
Q: How does Polyamide 66 compare to other thermoplastics in terms of performance?
A: Polyamide 66 is a high-performance thermoplastic with several properties, including excellent mechanical strength, wear resistance, and low frictional properties. It tends to absorb moisture, which can impact some physical properties, but its overall performance is superior in many industrial applications.
Q: What is the stock program availability for Polyamide 66 products?
A: The stock program for Polyamide 66 products, such as tecamid® 66 by Ensinger, ensures that a wide range of sizes and forms are readily available to meet the needs of various industries. Users should know that stock availability might vary based on specific requirements and market demand.
Q: How do monomers used in Polyamide 66 affect its properties?
A: The monomers used in Polyamide 66, specifically hexamethylene diamine and adipic acid, contribute to its excellent mechanical properties. These monomers result in a polymer chain with high strength and toughness, making Polyamide 66 suitable for various demanding applications.
Q: Can Polyamide 66 absorb moisture, and how does this affect its use?
A: Polyamide 66 can absorb moisture, which users should be aware of as it tends to impact some of its physical properties, such as dimensional stability and mechanical strength. Despite this, it remains a preferred choice for applications requiring high performance.
Q: What are some notable characteristics of Tecamid 66 by Ensinger?
A: Tecamid 66 by Ensinger offers excellent mechanical properties and is known for its outstanding wear resistance and low frictional properties. It is a high-performance polyamide pa66 that serves numerous industrial applications where reliability and durability are crucial.