304L stainless steel strips are known for their adaptability and strength, which makes them useful in many industries. This blog post intends to be an all-inclusive guide to 304L stainless steel strips, detailing their features, wide-ranging applications, and offered benefits. Also, we shall discuss the characteristics of a good manufacturer or supplier and the criteria for choosing the strips that will satisfy your tailored requirements. This guide will help industry veterans and newcomers make better choices for stainless steel materials.
What Makes 304L Stainless Steel Strip Different from Standard 304?
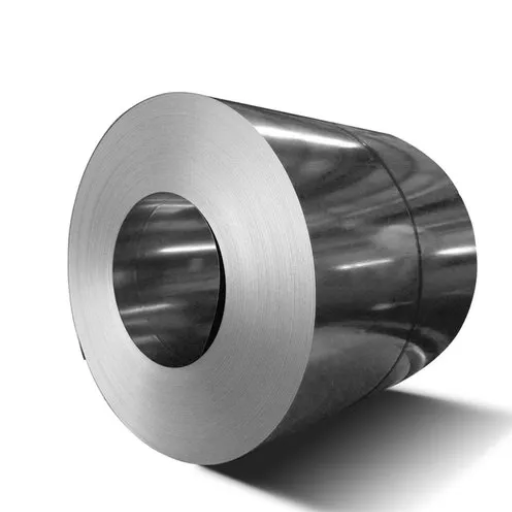
The carbon percentage significantly differs between 304L stainless steel and the standard 304. Since 304L has a lower carbon percentage, the danger of carbide precipitation forming during welding is considerably smaller. That makes 304L ideal for any application with extensive welding requirements, as it reduces the likelihood of corrosion at weld joints. Furthermore, enhanced resistance to intergranular corrosion due to lowered carbon levels improves durability in particular environments. While both grades have superb strength, resistance to corrosion, and versatility, 304L is preferable for applications requiring extensive weldability while maintaining structural integrity.
Understanding the Carbon Content in 304L vs 304 Stainless Steel
The main distinction between 304L and 304 stainless steel is their difference in carbon content. 304L has a maximum carbon content of 0.03%, while 304 has up to 0.08%. The reduced carbon level in 304L increases its resistance to carbide precipitation during welding, which can cause intergranular corrosion. This makes 304L more favorable for applications involving structural welding since it maintains its integrity and resistance to corrosion after welding and does not require post-weld heat treatment.
In comparison, 304 stainless steel, with higher carbon content, has a slightly higher tensile strength. However, it is also more susceptible to carbide precipitation due to elevated temperatures, especially during welding. While both grades are excellent regarding overall strength, corrosion resistance, and versatility, the selection between 304 and 304L boils down to application requirements such as the presence of welds, operational temperature, or corrosive environment.
Corrosion Resistance Benefits of 304L Stainless Steel Strip
The low carbon content in the 304L stainless steel strip helps minimize carbide precipitation during welding, which could otherwise lead to corrosion. Thus, it offers remarkable corrosion resistance. Additionally, 304L performs exceptionally well in various environments, including severe chemical, acid, and chloride-rich marine applications. Its ability to maintain resistance in highly moist industrial or corrosive environments makes it reliable for long-term durability and performance.
Typical Applications for 304L vs 304 Stainless Steel
Industries worldwide use 304L and 304 stainless steel; however, their applications may differ slightly owing to their properties.
Stainless 304 is quite popular in manufacturing kitchen appliances, automobile trim, paneling, and other fasteners. It is also powerful and has some corrosion resistance, giving it an edge over other general-use application options.
Extreme long-term exposure to high temperatures makes 304L stainless steel ideal for parts used in chemical processing and marine environments. It is more resistant to extreme conditions. With a lower level of carbon, it is a preferred choice in welding to prevent carbide precipitation.
Both types are remarkably versatile, but 304L’s improved weldability and resistance to sensitization make it better suited for structural work in industries with high environmental demands.
How to Choose Between Cold Rolled and Hot Rolled Stainless Steel Strip?
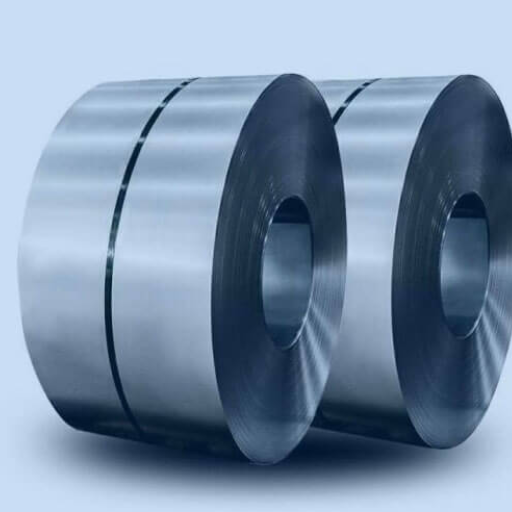
Selecting between cold-rolled and hot-rolled stainless steel strips should always be concerned with the application’s specifications. Cold-rolled stainless steel’s superior surface finish, tighter tolerances, and greater strength warrant its use in precision-driven and aesthetically sensitive fields such as automotive parts and consumer products. In contrast, hot-rolled stainless steel is more cost-effective and better suited for structural purposes or free areas where surface polish is not as critical. To make the best choice, evaluate the requirements and parameters like strength, finish, budget, and intended use.
Advantages of Cold Rolled Stainless Steel Strip Manufacturing
The process of manufacturing cold-rolled stainless steel strips comes with numerous valuable advantages across multiple industries.
Awarded Finish: Cold-rolled stainless steel strips greatly benefit from its rolling processes. This is achieved at a remarkable rate, making the material perfect for cosmetic and precision-essential operations on electronics, surgical devices, and numerous consumer products.
Awarded Strength: Toughening of Stream bending arises from further filtering in mechanical tools, which is adopted by cold rolling due to increased rotary motion from the feeding direction. Also, the dimensional precision of parts after performing this step increases, allowing cold-rolled regions to be used for very intricate, high-precision tasks.
Width Control: This kind of rolled strip is manufactured with width control that permits tighter tolerances for uniformity during repetitions. This impacts industries like automotive and aerospace, which emphasize high-priority engineering standards.
Long-Term Value: As mentioned above, the initial production doors of cold-rolled stainless steel may be higher. However, the sheer strength, resistance to corrosion, durability, and optimized maintenance are unrivaled in highly demanding applications, lowering costs and enhancing value in the long run.
Adaptability and Personalization: The procedure permits an extensive list of sizes, grades, and finishes, which helps meet different requirements across numerous industries. It also allows the creation of materials useful for particular applications.
Cold-rolled stainless steel strips enable industries to meet higher quality standards, operational efficiency, and product value for more advanced, challenging markets.
When to Use Hot Rolled Stainless Steel for Your Project
Hot-rolled stainless steel would be appropriate for construction, automotive, or heavy machinery projects requiring high-strength, durable materials. I would consider using it for projects that do not need precision dimensions since such processes tend to create minor deviations. It is also advantageous for large-scale applications because it incurs lower production costs than cold-rolled alternatives. Furthermore, hot-rolled stainless steel is remarkable in applications necessitating extreme environments or high temperatures and endurance, applying it to harsh industrial requirements.
Surface Finish Options for 304L Stainless Steel Coil (BA, 2B)
The surface finish of 304L stainless steel coil also plays an essential role in defining its aesthetic appeal, suitability for different applications, and corrosion resistance. This BA (Bright Annealed) finish has a smooth and reflective surface obtained by annealing in a controlled atmosphere to avoid scaling. Due to its eye-catching nature and easy cleaning, the BA finish works well in decorative kitchen equipment and appliances.
In contrast, a 2B finish is a matte and somewhat reflective surface produced by cold rolling followed by annealing, pickling, and skin passing. It has outstanding hygiene and corrosion resistance, making it appropriate for industrial and food-grade applications. Both finishes augment the adaptability of 304L stainless steel, which helps meet its functional and aesthetic requirements.
What Other Stainless Steel Grades Are Available Besides 304L?
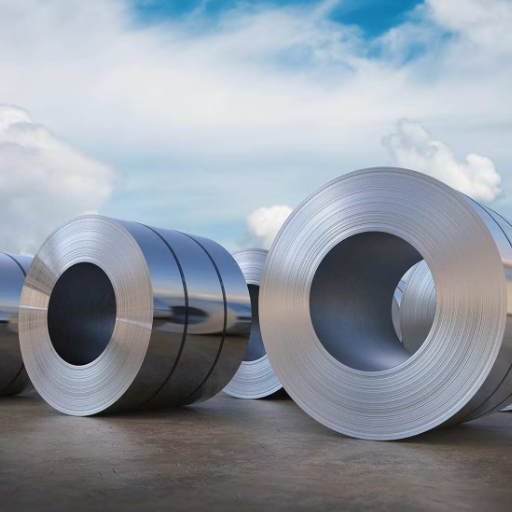
Besides 304L, other stainless steel grades are available, each with specific applications. Alternatives include 316L, which is even more corrosion-resistant, especially in oceanic or chemical facilities. Grade 430 is relatively inexpensive with fair corrosion resistance, mainly used for interior applications. There are also other grades for higher temperature applications, like 310S, which has remarkable heat resistance. Duplex stainless steels like 2205 have great strength and excellent corrosion resistance, making them suitable for harsher environments. The choice of stainless steel grade is guided by the requirements for its corrosion resistance, strength, and operating conditions.
316L Stainless Steel Strip: Properties and Applications
316L stainless steel strip is a low-carbon grade of 316 stainless steel and maintains excellent corrosive resistance, especially in chloride-containing oceans and chemicals. The low carbon content lowers the chances of carbide precipitation during welding, which improves the material’s critical usability. The primary characteristics of 316L are high strength, outstanding ductility, high resistance to pitting as well as crevice corrosion, and remarkable performance in high temperatures. This makes it a good candidate for use in heat exchangers, medical devices, and pharmaceutical machinery.
Because of its usefulness and strength, the 316L stainless steel strip is used across many industries. It often produces surgical devices, machinery, and food service equipment. Its harsh environment resistance makes it useful for marine applications such as boat fittings and underwater components. Its pleasing appearance and resistance to discoloring also make it a widely preferred material for construction.
430 Stainless Steel vs 304L: Which Grade to Choose?
Comparing 430 stainless steel to 304L, each choice has advantages depending on the intended use and surrounding conditions. 430 is a ferritic stainless steel known for its low cost, good corrosion resistance, and formability. Thus, it is often used in kitchen appliances, automotive trims, and other decorative applications. However, its resistance to corrosion and heat is not on par with austenitic grades, which is why 304L serves better.
Meanwhile, 304L, a low-carbon version of the famous 304 stainless steel, is far more durable due to better corrosion resistance and weldability. Because of these, 304L is vastly used in chemical processing, marine equipment, and areas exposed to moisture or acids. Primarily available at a premium, switching to 304L has its benefits due to unmatched durability and versatility for harsh and demanding workloads.
In summary, opt for 430 in less demanding, budget-sensitive projects. If relocating to more excellent environments exposed to heat, corrosion, or welding, 304L serves better.
201 and 321 Stainless Steel Options from Our Factory
201 Stainless Steel: Type 201 stainless steel has an alloy composition of high manganese and low nickel. The type offers reasonable strength with some corrosion resistance in moderately corrosive environments. Therefore, it is used in less expensive kitchen utensils, automobile trims, sinks, etc. It is best suited for places with mild corrosive environments, though, due to cost efficiency, it may underperform against highly corrosive or high-temperature conditions compared to other grades.
321 Stainless Steel: Type 321 stainless steel has titanium added to improve intergranular corrosion resistance. It is mainly used in aerospace industries and the construction of heat exchangers and exhaust systems because it can endure long periods of exposure to high temperatures without losing strength or structural integrity.
We manufacture and sell 201 and 321 stainless steel products with professional design, manufacture, and industrial consultancy support. Whether you need affordable materials with moderate heat and corrosion resistance or parts that require superior performance, we guarantee all products will meet the requirements, supported by our extensive experience in professional consultation and manufacturing.
How Does Our 304L Stainless Steel Strip Factory Ensure Quality?
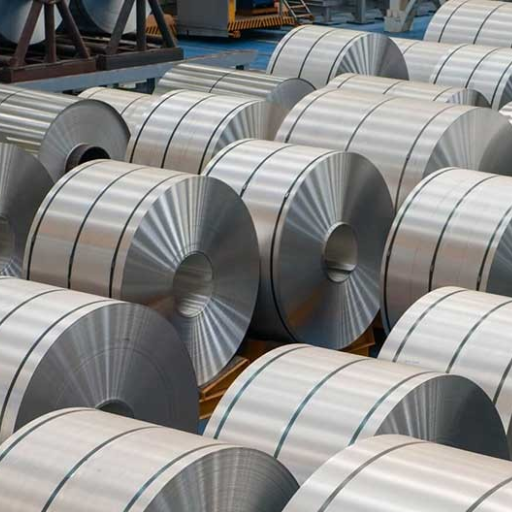
Our 304L stainless steel strip factory combines raw material procurement controls, advanced technology, and quality management systems to ensure the utmost quality. All raw materials undergo stringent inspection processes to ascertain compliance with relevant standards, while cutting-edge equipment can execute operations accurately and precisely. Each strip undergoes exhaustive testing, including but not limited to tensile strength, corrosion resistance, and dimensional checks, to ensure that unrivaled customer satisfaction standards are consistently achieved. In addition, compliance, satisfaction, and trust for the customer are ensured by maintaining certification and international quality standards.
ASTM A240 Compliance and Quality Standards
The specification scope includes stainless steel chromium and chromium-nickel alloys in plates, sheets, and strips for pressure vessels and other applications: ASTM A240. This specification outlines mechanical properties and chemical composition requirements to guarantee operational reliability and structural and performance endurance. The materials stated in the scope of the ASTM A240 are required to possess significant tensile strength and resistance to corrosion, as well as strict control over dimensional tolerances if they are to be used in highly stressed environments. Manufacturers must document concrete quality control procedures, such as checking materials and holding registered certification from deemed authorities. Compliance with these requirements ensures that products covered by these standards of ASTM A240 establish adequate reliability alongside dependability when used for critical industrial applications.
Precision Stainless Steel Manufacturing Capabilities
Manufacturing precision components from stainless steel involves advanced technology and processes to meet high quality and performance standards. Among the capabilities are advanced techniques for precision cutting, CNC machining, and forming, which enable the manufacture of components with intricate geometries and high precision. Specialized coatings and finishing processes such as polishing, grinding, and coating are tailored to durability and aesthetics for the specified surface requirements. Also, manufacturers apply modern quality control techniques such as non-destructive testing (NDT), which allows for the evaluation of the parts’ strength, corrosion resistance, and dimensional accuracy. With these capabilities, the manufacturers serve the aerospace, automotive, medical, and energy industries that require custom stainless steel solutions that need high reliability and precision.
What Specifications and Formats Are Available for 304L Stainless Steel?
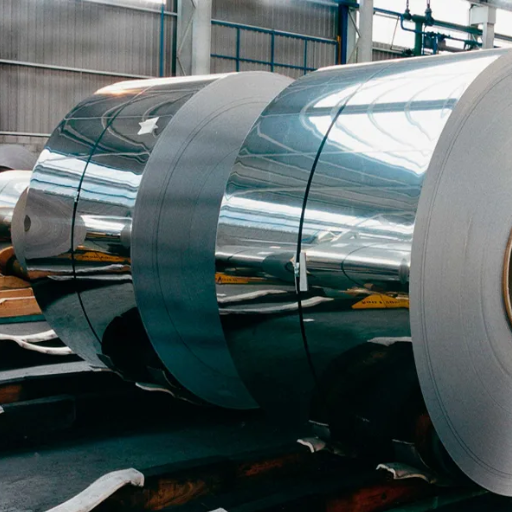
304L stainless steel is offered in various specifications and forms to accommodate different application needs. The most common specifications for sheets, plates, bars, and pipes are ASTM A240, ASTM A276, and A312. It is supplied in different forms, such as coils, sheets, plates, bars, pipes, tubing, and cut or machined tailored parts. Depending on the intended purpose, the material can be supplied in a mill or brushed or polished finish.
Stainless Steel Coil Strip Dimensions and Tolerances
Stainless steel coil strips are commonly found within the range of 0.1mm to 6mm for thickness and 10mm to 2000mm for width, depending on the manufacturer’s capability and individual requirements. A range of thickness tolerances is usually set within ±0.02mm to ±0.05mm, while width tolerances tend to be more relaxed at ±0.1mm to ±0.2mm. Dimensional tolerances are also defined by the standard and the type of finish requested, with tighter tolerances available for precise engineering applications. Often, customizable options are available, making them ideal for use in construction, automotive, and other manufacturing industries.
Customization Options for 304L Stainless Steel Sheet Plate
For 304L stainless steel sheet plates, I can confirm that customization tailored to individual needs is available, making it easy to adjust for a wide range of requirements. All dimensions undergo adjustments by specified tolerances, ensuring all requirements are fulfilled. Brushed, polished, and mill finishes are also customizable, highlighting specific functional and aesthetic requirements. Furthermore, we offer matching custom design solutions with advanced industrial and architectural precision through laser, bending, cutting, and other fabrication services. Customization across the board guarantees high-quality results, whether the requirement is industrial or architectural, paving the way for standards you expect, not what you have to settle for.
Why Choose Our Factory as Your Stainless Steel Strip Supplier?
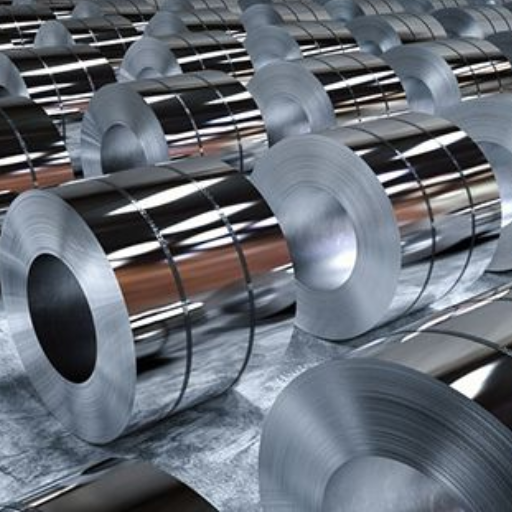
Our factory is unrivaled in supplying stainless steel strips because of the precision our quality and customization processes meet and our customer’s satisfaction. We adhere to all relevant compliance standards within their industry by using advanced manufacturing technologies as precision products require. We can swiftly meet your unique project requirements because of the multiple finishes, processing methods, and dimensions we can work with. Our support team guarantees timely support communication and reliability with stainless steel service, making every step toward you seamless.
Competitive Pricing for Wholesale 304L Stainless Steel
Price becomes secondary when dealing with the wholesaled 304L stainless steel to maintain the competitive value our company offers. Our years of collaboration with suppliers enable us to provide cost-effective solutions without compromising quality due to our unstreamlined manufacturing processes tailored to your needs. We provide constant stock availability alongside transparent prices, so every reliability and affordability is indeed present from us in all transactions.
Manufacturing and Supply Chain Advantages
Both efficiency and quality are integrated into our supply chain and manufacturing processes. Using state-of-the-art advanced manufacturing methods, we produce 304L stainless steel with unrivaled silicone precision, guaranteeing structural reliability and durability in every batch. Furthermore, our strategic collaboration with suppliers worldwide allows us to foster working relationships to obtain high-quality raw materials at favorable prices. This balanced supply chain guarantees sustained inventory levels and rapid fulfillment times, which boosts your business prospects in meeting project deadlines. Sustainability and transparency are at the core of our operations, which focus on continuously refining processes for waste reduction and lowering the carbon footprint.
References
Frequently Asked Questions (FAQ)
Q: What is the difference between 304 and 304L grade stainless steel?
A: 304 and 304L stainless steel strips differ primarily in carbon content. 304 contains up to 0.08% carbon, while 304L has a lower carbon content (typically 0.03% max). This lower carbon content in 304L makes it more resistant to intergranular corrosion after welding. Both grades offer excellent corrosion resistance, but 304L is preferred for applications where welding is required. Many manufacturers and suppliers in China produce both variants, with 304L being slightly more expensive but offering enhanced weldability and corrosion resistance in specific environments.
Q: How does 201 stainless steel compare to 304 stainless steel?
A: 201 stainless steel contains less nickel than 304 stainless steel, which is replaced with manganese and nitrogen. While 304 offers superior corrosion resistance and formability, 201 is more economical. 304-grade stainless steel is widely used in food processing, chemical containers, and architectural applications, whereas 201 stainless steel is typically used in less demanding environments like interior applications, household goods, and decorative items. For critical applications requiring maximum corrosion resistance, 304 is generally recommended over 201.
Q: What are the typical applications for 304 stainless steel strips?
A: 304 stainless steel strip is widely used across numerous industries due to its excellent corrosion resistance and formability. Typical applications include food processing equipment, kitchen equipment, architectural trims, automotive parts, chemical containers, heat exchangers, and pipe tube components. This versatile material is also used in medical equipment, springs, and stainless steel cable ties-ball self-locking systems. The 304 2B finish is particularly popular for applications requiring a smooth, semi-reflective surface. The material’s durability and resistance to many chemicals make it ideal for industrial steel applications in demanding environments.
Q: How does 316 stainless steel differ from 304L stainless steel?
A: 316 stainless steel contains 2-3% molybdenum, giving it superior corrosion resistance to 304L, particularly against chlorides and salt environments. While both are austenitic stainless steels with excellent formability, 316 offers better resistance in marine and chemical processing environments. 304L is more economical and widely used in general-purpose applications, while 316 is preferred for coastal environments, marine applications, and chemical processing. Both grades are available from most stainless steel strip manufacturers, but 316 typically commands a premium price due to its enhanced properties and higher molybdenum content.
Q: What is the chemical composition of a precision cold-rolled 304L stainless steel strip?
A: Precision cold rolled 304L stainless steel strip typically has a chemical composition of 18-20% chromium, 8-12% nickel, maximum 0.03% carbon, maximum 2% manganese, maximum 1% silicon, maximum 0.045% phosphorus, maximum 0.03% sulfur, with the balance being iron. This low-carbon variant of 304 stainless steel offers excellent corrosion resistance while maintaining good weldability. The precise control of chemical composition by reputable manufacturers and suppliers in China ensures consistent quality in the finished strips, making them suitable for demanding applications requiring tight tolerances.
Q: How does 430 stainless steel coil compare with 304 stainless steel strip?
A: 430 stainless steel coil is a ferritic stainless steel containing 16-18% chromium with no significant nickel content, whereas 304 stainless steel strip is an austenitic grade containing both chromium (18-20%) and nickel (8-10.5%). The 430 grade offers good corrosion resistance but is less resistant than 304 in harsh environments. 430 stainless steel is magnetic, more economical, and typically used for indoor applications like appliance trim and decorative purposes. 304 offers superior corrosion resistance, better formability, and is non-magnetic, making it suitable for more demanding applications. Both are available from stainless steel strip manufacturers at competitive prices.
Q: What are the standard finishes available for 304 stainless steel strips for sale?
A: 304 stainless steel strip is available in several standard finishes from manufacturers and suppliers. The most common are: 2B (smooth, reflective finish achieved through cold rolling, annealing, and light rolling), BA (Bright Annealed – mirror-like finish), #4 (brushed finish with visible grain), #8 (mirror-like polished finish), and matte/dull finish. The 2B finish is widely used for general applications, while BA is preferred for decorative applications. China factory suppliers can also provide custom finishes according to customer specifications, including different roughness values and patterns. The price of stainless steel strips varies depending on the finish type.
Q: How can I contact the leading 304L stainless steel strip manufacturers for quotes?
A: To contact us or other leading 304L stainless steel strip manufacturers for quotes, visit the manufacturer’s website and fill out their contact form, email their sales department, or call their customer service line. When reaching out, be prepared to provide specifications such as dimensions (width, thickness, length), grade (304, 304L, etc.), finish type, quantity needed, and application details. China’s leading 304L stainless steel strip manufacturers and suppliers usually respond within 24-48 hours with pricing and availability information. Many manufacturers also attend industry trade shows where you can meet representatives to discuss your specific requirements.
Q: What factors affect the price of stainless steel cold rolled strips manufactured by manufacturers?
A: Several factors influence the price of stainless steel cold rolled strips: grade (304, 304L, 316, 201, etc.), thickness and width tolerances (precision cold rolled strips with tighter tolerances cost more), finish type (2B, BA, #4, etc.), quantity ordered (larger orders typically receive better pricing), raw material costs (particularly nickel and chromium prices), production complexity, certification requirements, and market conditions. Additionally, shipping costs, tariffs, and exchange rates can significantly impact the final price when sourcing from manufacturers and suppliers in China or other countries. For the most competitive pricing, contacting multiple strip suppliers and manufacturers directly for quotes based on your exact specifications is advisable.