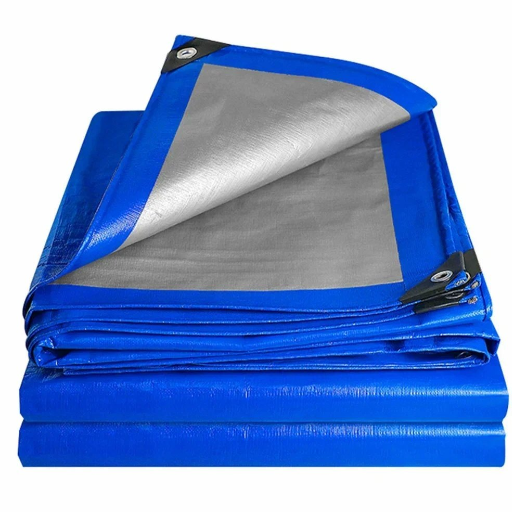
It’s essential to know how to select a manufacturer when dealing with tarpaulins of high-grade quality HDPE. In this post, I aim to provide a guide that will assist readers in navigating and grasping the primary aspects of the best suppliers of HDPE tarpaulins. Everything from the characteristics and advantages of tarpaulins to the reputation, manufacturing capability, and product range of the suppliers is included. Whether you are a business owner or an individual needing strong and dependable tarps, this article will aid you in attaining the information necessary to make the right choice.
What Is HDPE Tarpaulin and How Is It Different from Other Types?
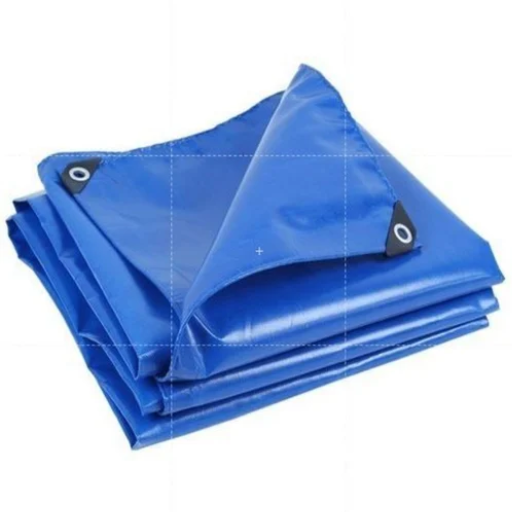
HDPE tarpaulin or High-Density Polyethylene tarpaulin is a type of tarp made of strong and flexible material consisting of high-density polyethylene fiber woven together and laminated with polyethylene sheets. Its exceptional strength, lightweight, water and tear-resistant properties, alongside its resistance to chemicals and ultraviolet rays, separate it from other tarpaulin types. In contrast with PVC tarpaulins, HDPE tarps are more environmentally friendly as they can be reused and negatively impact the ecosystem less. Due to these qualities, HDPE tarpaulin is the most preferred tarp in agricultural, industrial, and commercial fields.
Understanding High-Density Polyethylene Tarpaulin Materials
The most notable feature of High-Density Polyethylene (HDPE) tarpaulins is their durability and variety of uses. They are constructed by weaving HDPE fibers and applying laminated polyethylene sheets for strength and flexibility. Although the HDPE tarps are lightweight, making them easy to carry, they are powerful and offer superior resistance to tearing, puncturing, and environmental stress.
UV rays and long periods of sunlight do not damage HDPE tarpaulins, enabling their use in any weather condition without degrading over time. These materials are also water—and chemical-resistant, further increasing their applicability for harsh environments where long material endurance is required. Moreover, sein HDPE tarpaulins are recyclable, making them environmentally superior to materials such as PVC.
Their unique features enable an extensive application of HDPE tarpaulins in farming for crop protection, industrial settings for covering machines and materials, and commercial sectors for designing tents and shelters or using them as temporary storage facilities. Their unmatched durability while remaining lightweight and environmental sustainability provides an economic upper hand across numerous industries.
Comparing HDPE Tarps vs. PE Tarpaulin and LDPE Options
In the comparison of HDPE (High-Density Polyethylene) tarps with the PE (Polyethylene) and LDPE (Low-Density Polyethylene) options, the differences appear to be in the durability, strength, and applications. HDPE tarps have superior strength and tear resistance due to their woven design and high-density structure. These are more rigid, weather resistant, and long-lasting, which makes them ideal for heavy-duty uses such as construction covers, agricultural uses, and industrial storage.
The opposite is true for PE tarpaulins, including LDPE and other polyethylene forms. These tend to be lighter and more flexible. On the other hand, LDPE tarps are softer but less durable and more prone to damage with more significant stress or lousy weather. Their application is typically better suited for covering furniture mids and providing temporary waterproof seals than more demanding tasks.
In general, while HDPE excels in performance for heavy-duty, long-term use, PE and LDPE offer an economical resolution for lightweight, short-term purposes. Selecting the correct option depends upon the particular strength, budget, and longevity requirements, all of which will influence the final decision.
Benefits of Woven HDPE Fabric in Tarpaulin Manufacturing
Woven HDPE fabric is one of the popular features due to its remarkable strength and long-lasting qualities used in making tarpaulins. The woven structure of the tarpaulin HDPE features gives ample tearing, stretching, and puncturing protection, ensuring its durability when exposed to challenging conditions. Besides, HDPE tarpaulins are lightweight and sturdy, which allows for effortless handling and deployment without performance setbacks.
Woven HDPE fabric’s most striking properties feature resistance to harsh weather, UV rays, and water. The material does not allow water to seep in and stand consistent sunlight for long periods, guaranteeing durable, functional efficiency. Moreover, woven HDPE fabric is recyclable, eco-friendly, and offers better sustainability options than synthetic materials. These remarkable features make the HDPE fabric ideal for industrial and personal use, adding to its versatility. These defining qualities make HDPE fabric popular in agriculture, construction, and logistics.
How to Choose a Reliable HDPE Tarpaulin Manufacturer?
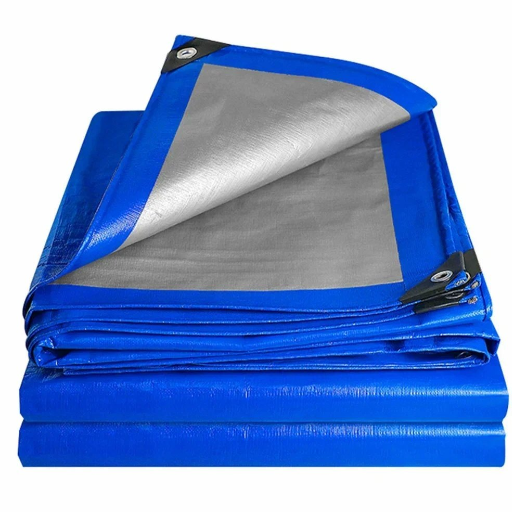
Consider starting with the reviews and reputation of an HDPE tarpaulin manufacturer. It is essential to check if they consistently have quality products. Check their production processes and certifications to verify if they comply with safety and quality measurements relevant to your needs. In addition, check if the tarpaulins offered meet the required specifications and are strong enough to serve the purpose intended. The manufacturer should also provide unambiguous charges, reasonable warranty lengths, effective customer service, and access upon request. Most importantly, focus on those with a good history of fulfilling orders and that are environmentally friendly.
Identifying Leading Manufacturers of HDPE Tarpaulin Worldwide
When mentioning the best HDPE tarpaulin manufacturers globally, it is also imperative to note the key market players that offer exceptional products and services.
Cosmoplast Industrial Company LLC (UAE) is one of the strongest players in quality and durability. It offers various HDPE tarpaulin solutions for industrial, agricultural, and commercial purposes. Cosmoplast’s certifications meet international requirements regarding safety and environmental norms. The company focuses on customer support, provides quality services at reasonable prices, and ensures timely delivery.
Shree Tarpaulin Industries (India) Shree Tarpaulin is one of India’s largest HDPE manufacturers and exporters. The company is acclaimed for its increasing product range and customization capabilities. Their products are known for being lightweight yet highly durable, waterproof, UV-resistant, and cost-effective. The company also implements a sustainable development policy without compromising the quality of its services.
KSA Polymer (China) is one of the top HDPE tarpaulin producers in the world. It offers advanced designs and high-performance solutions for various industries. Its products are crafted using modern technology, which improves reliability and weather resistance. KSA Polymer is known for its transparent pricing and well-developed logistics network, enabling it to meet global delivery expectations.
By relying on these manufacturers, one can always be assured of the longevity and quality of the HDPE tarpaulins that best suit all application needs.
Evaluating Tarpaulin Factory Quality Standards and Certifications
Several factors need to be considered when reviewing the tarpaulin factory’s certifications and quality standards. First, the factory must be certified with at least ISO 9001, indicating a high-quality management level. This certification shows minimal defects in product output and that the customer’s needs are met. Compliance with ISO 14001 also shows concern regarding environmental impacts due to manufacturing processes.
Moreover, product-specific certifications like REACH compliance should be considered, guaranteeing the materials’ safety and environmental friendliness. Compliance with international safety standards (fire retardancy certification, for example) adds value to the reliability of the tarpaulins, especially for industrial and high-risk areas. Continuous auditing, third-party testing, and client reviews give a good impression of the factory’s dedication to achieving standards of quality and responsibility.
What to Look for in a HDPE Tarpaulin Supplier
Material Quality and Durability: For the given task, select a supplier that sells high-quality, UV-resistant, waterproof, and tear-resistant HDPE tarpaulins. These qualities are essential for tarpaulins in harsh environments since they help ensure reliability and endurance.
Compliance with Industry Standards: Do not use suppliers without international certifications, ISO 9001, compliance with REACH, and fire retardancy. These certifications guarantee that the products provided are safe, eco-friendly, and suitable for advanced usage.
Custom Options: A suitable supplier allows size, thickness, and color customization to meet different application requirements. Depending on project specifications, they should also be customized to allow for eyelets, reinforced edges, or laminations.
Reputation and Reliability: Check the supplier’s reputation by examining reviews, case studies, and testimonials. A reputable supplier will always maintain the expected quote, timeliness in service, and after-sales customer service.
Cost and After-Sales Support: While value is significant, it should not compromise quality. An ideal supplier provides comprehensive after-service support in terms of warranties, repairs, guidance for maintenance, or installations.
Through keen analysis of the stated factors, an appropriate supplier of HDPE tarpaulins with the required quality and business standards will be found.
What Are the Key Features of Premium Quality HDPE Tarpaulin?
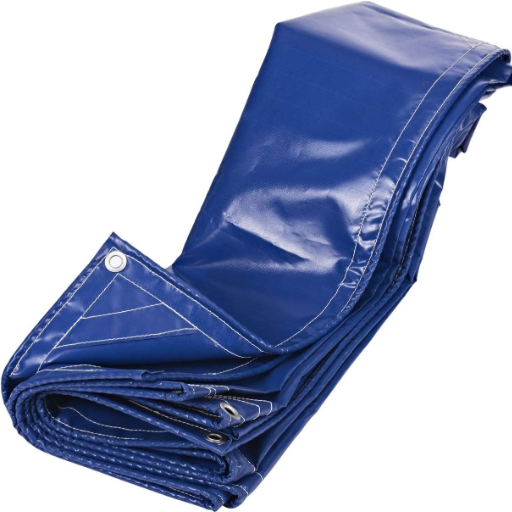
The high-density polyethylene construction guarantees excellent tensile strength and tear resistance. Premium-quality HDPE tarpaulins have several notable features that underscore their unparalleled all-purpose durability. Furthermore, they are waterproof, making their use ideal across various agriculture, construction, and transportation industries. Premium HDPE tarpaulins are UV-stabilized, which protects them from sunlight and prolongs their lifespan even under severe weather conditions. Also, these tarpaulins are lightweight yet supremely durable, allowing for effortless maneuverability without diminishing performance.
GSM Ratings and Thickness: What Do They Mean?
GSM, or grams per square meter, quantifies the weight and density of the fabric material used in tarpaulins. Moreover, every GSM value indicates a specific characteristic. A higher GSM value indicates thick and more resilient tarpaulins, while lower GSM values signify not only more lightweight but also more flexible options. For instance, a rating of 90-120 marks the lighter side as ideal for temporary use. On the other hand, tarpaulins with GSM ratings exceeding 200 are heavy-duty and more suitable for demanding applications like agricultural or industrial coverage.
The thickness of a tarpaulin is pivotal in determining its overall durability, resistance to external factors, and external wear and tear. Thicker tarpaulins protect better against wear and tear, punctures, and harsh weather. The appropriate GSM and thickness have to be chosen according to the specific use case, balancing rigidity with flexibility and ease of handling. Knowing these metrics is essential in selecting the right tarp to fit one’s needs.
UV Protection and Waterproof Capabilities in HDPE Tarpaulin
HDPE tarps are made with specially formulated UV protection and waterproofing capabilities. Incorporating UV stabilizers during manufacturing allows the material to resist deterioration from the sun and increases the lifespan of the HDPE tarpaulin under harsh sunlight. This feature makes these tarps suitable for outdoor use.
HDPE tarps are also coated with layers of water-repellent materials, which ensures that the objects or areas covered are safe from rain and moisture. Their water-resistant properties increase their durability and versatility in construction, agriculture, and transport. By combining UV protection and waterproofing, these tarps significantly improve their ability to withstand harsh and demanding environmental conditions while preserving reliability.
Durability Factors: Multiple Layers and Laminated Tarpaulin Construction
The strength of tarpaulins, especially those made of HDPE, is enhanced tremendously by adding more layers and using laminated construction. These layers often include a reinforced woven core encased in protective coatings, resulting in a flexible and resilient material. Laminated tarpaulins are custom-made to prevent tearing, abrasion, and other mechanical stress, which makes these tarps perfect for heavy-duty applications. Integrating numerous layers with lamination increases the tensile strength and the resistance to UV radiation, water, and elements, allowing the tarpaulin to perform optimally over time. This construction technique preserves durability even in demanding industrial and outdoor settings.
What Range of HDPE Tarpaulin Products Are Available?
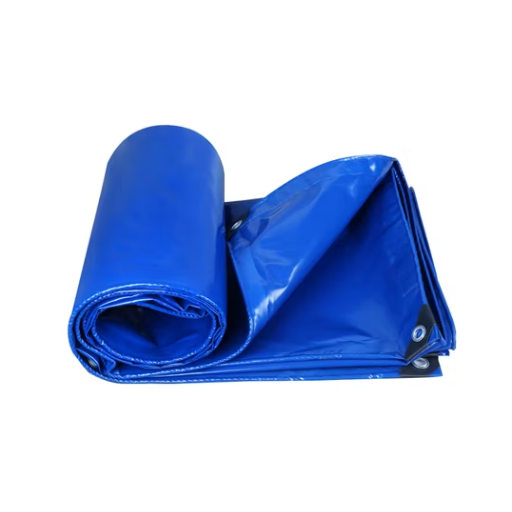
Ranging in size, thickness, and color for various applications, HDPE tarpaulin products are readily available. Options include lightweight tarps for temporary purposes, medium-weight for general use, and heavy-duty tarp variants designed for industrial and agricultural applications. Protective features such as UV protection, waterproofing, and edge reinforcements can also be tailored. There are often many customization options to adhere to unique specifications.
HDPE Tarpaulin Sheets vs Rolls: Which to Choose?
The decision is primarily based on the specific requirements for use. HDPE sheets are pre-cut to standard sizes and are convenient when covering equipment, construction sites, or agriculture. They are also time-saving when a ready-to-go solution is required. Alternatively, for projects of specific or unconventional measurements, HDPE tarpaulin rolls give customized dimensions flexibility. Ideal for extensive roofing or wrapping in industrial settings, rolls are preferred for large-scale or continuous applications. Overall, the choice comes down to immediate application convenience versus customizability for tailored solutions.
Heavy-Duty Tarpaulin Options for Industrial Applications
Heavy-duty tarpaulins are crucial for many industries due to their long life, versatility, and ability to withstand different weather conditions. A coating, material, and thickness must be considered to find the best fit. Heavy-duty tarpaulins are usually made from polyethylene(P), high-density polyethylene (HDPE), or polyvinyl chloride (PVC). Each material provides different advantages; HDPE offers an extremely light but strong material, while PVC delivers excellent protection against harsher chemicals and environmental conditions.
In construction, transportation, and storage, these tarps are used alongside other protective features like UV resistance, waterproof coatings, and tear resistance to protect them from extreme wear and exposure. Further customization comes in the form of customizable rolls or pre-sized sheets. Wrapping goods during transit, shielding vehicles or equipment, and covering construction sites are some popular uses. To further enhance effectiveness, choosing the correct weight defined in grams per square meter (GSM) and adding reinforced edges with grommets promotes ease of use.
Specialized Products: Pond Liners and Water Storage Solutions
In terms of pond liners, pocket ponds usually require good-quality materials, such as EPDM or HDPE, because of their considerable strength, resiliency to ultraviolet rays, and holes. These liners can be used for decorative and functional ponds, retaining water without leakage effectively. On the other hand, prefabricated tanks and custom-built systems serve as excellent options for water storage solutions depending on one’s site constraints and requirements. It ensures durability but combines optimal flexibility, temperature resistance, and environmental conditions like with these systems for enhanced, long-lasting performance.
How Can I Customize HDPE Tarpaulin for Specific Requirements?
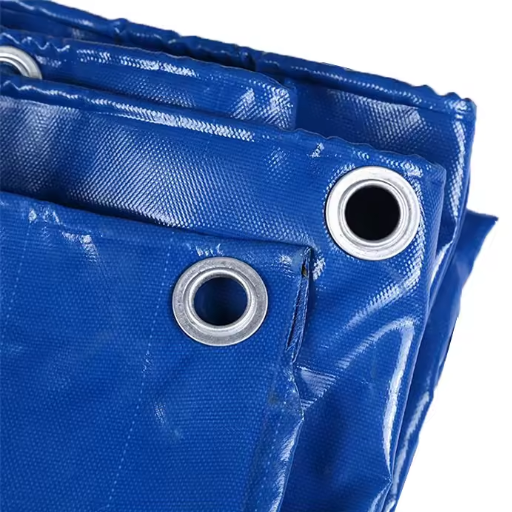
Custom HDPE tarpaulin can be designed to suit client specifications for size, thickness, and other defining features. Customizable dimensions make it worthwhile for application in ponds, greenhouses, or other industrial covers. Other customization options, such as reinforced edges, UV stabilization for prolonged outdoor use, and robust eyelets or grommets, enhance secure fittings. Manufacturers ensure the tarpaulin meets unique requirements by adding preferred colors, fire retarding materials, or anti-slip surfaces, making the tarpaulin effective in performing its intended tasks.
Available Sizes, Colors, and Specifications from Manufacturers
Block tarps are manufactured in a wide range of sizes, from small six by 8 feet to large coverage areas that can exceed 100 by 100 feet. A range of thicknesses, from lightweight five mils to heavy-duty 20 mils or more, is also available to cater to different needs.
Custom branding quickly offers versatile color options. Standard colors are Blue, Green, Black, and Silver. Specialized tarpaulins can also have spyware or camouflage patterns.
Some features include waterproof and mildew-resistant coatings, reinforced hems with grommets, UV protection, and rust-resistant grommets. Some products may consist of fire-retardant or chemical-resistant surfaces for industrial use, while others are enhanced. Customization options are frequently offered to align with a specific set of requirements or requests from the client.
Custom-Made HDPE Tarps: Process and Possibilities
Like all custom products, design starts with material selection, which includes thickness, dimensions, color, and special coatings such as UV resistance, waterproofing, and flame retardancy. The clients can specify exact measurements and features such as reinforced borders, grommet strategic placements, or even specific nontraditional forms.
Using state-of-the-art machinery, producers precision cut and seal the fabric to specific dimensions, resulting in performant reinforced seams. Some providers offer add-ons such as branding or logos for commercial purposes.
Along with industrial-grade containment and agricultural use, recreational-grade tarps, such as shading structures and custom covers, are also available. Meeting design customization ranging from performance, safety, and aesthetics ensures these tarps serve the purpose of large—and small-scale projects.
What Are the Cost Considerations When Buying from HDPE Tarpaulin Manufacturers?
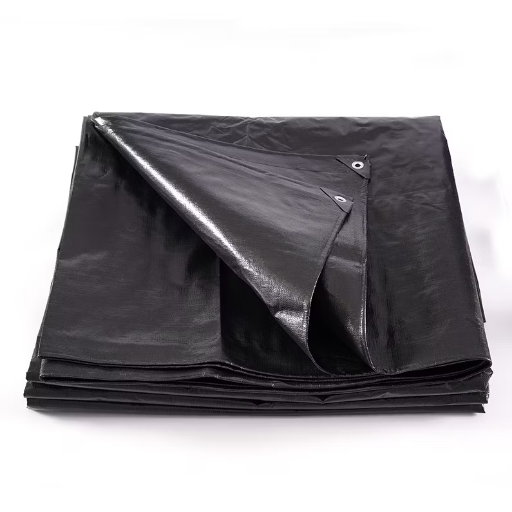
When determining the cost of HDPE tarpaulins, consider the material quality, thickness, and durability, as each impacts the price. Customization options like size, color, and branding may increase costs. Typically, bulk orders lower the price per unit, making them cheaper for larger projects. Shipping costs and lead times must also be included because they may differ from the manufacturer’s location and the order size.
Pricing Factors: Raw Material, GSM, and Manufacturing Process
It is well known that product pricing is related to the raw materials used. Better materials can improve durability and performance, making the product more expensive. GSM (grams per square meter) is substantial because it defines the thickness and weight of the material. Higher GSM generally means a more efficient product but will increase production costs. The manufacturing process is also essential. More complex processes using advanced machinery tend to cost more, while more straightforward methods may reduce overall expenses. These factors will influence the choices made regarding quality requirements and budget.
Finding Cost-Effective HDPE Tarpaulin Without Sacrificing Quality
To buy cost-effective HDPE tarpaulin while maintaining quality, thoroughly research the manufacturer or supplier’s ratings. ‘100% virgin HDPE’ should be indicated on the tarpaulin as it makes the product more durable and resistant to wear and tear. Make sure to check the GSM rating or grams per square meter of the tarp, as it should meet the requirements of strength and thickness. It is noted that 150-250 is optimal for almost all purposes due to cost efficiency.
Also, check the prices from multiple suppliers and ask about discounts for bulk purchases. Inquire about UV stabilization and lamination to protect the tarp from sun and water damage. Finally, checking if the supplier issues proper certifications, such as ISO or quality assurance standards, can help guarantee product reliability and certifications while being budget-friendly.
Bulk Orders and Wholesale Options from Tarpaulin Suppliers
When pondering bulk orders and wholesale options for HDPE tarpaulins, it is essential to consider suppliers with reasonable pricing, dependable quality, and speedy delivery. Most manufacturers offer discounts for upper-limit orders, thus bringing down the cost per unit. Additionally, wholesalers mainly serve the needs of their customers by providing customization, such as particular size and color, and additional durability, such as UV resistance or reinforced edges.
Top suppliers offer changeable prices and an easy ordering procedure. They provide bulk pack sizes, guaranteeing adequate stock for agriculture, construction, transport, etc. Delivery logistics are further refined for speedy and secure shipping, especially for international clientele. With the aid of numerous reputable suppliers, customers get value for their money by reading reviews and directly communicating with the sales team for the best deals.
Why Choose a Chinese HDPE Tarpaulin Manufacturer?
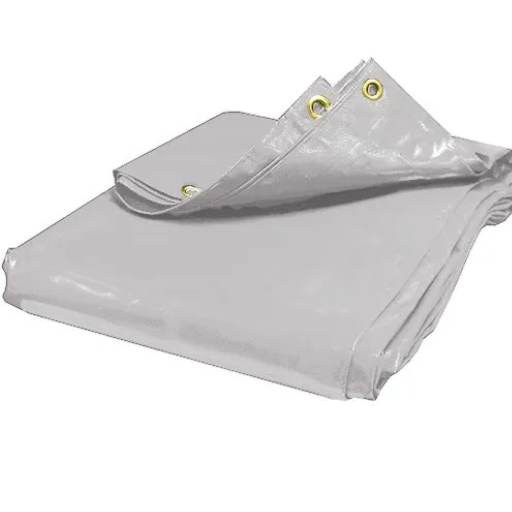
The Chinese HDPE tarpaulin manufacturers are distinguished by their high-quality products that are competitively priced. These manufacturers use new technologies and optimized production processes to meet client needs with custom designs, specified requirements, bulk orders, and many other customization options. Through years of operational experience in large-scale industries, they are always on time on tight schedules while maintaining proportionality with product standards, consistency, and quality. Additionally, most Chinese manufacturers comply with international quality certifications, making them a favorable option for international buyers looking for good deals and trusted solutions.
Advantages of Working with Tarpaulin Manufacturers in China
There are numerous benefits to working with Chinese tarpaulin manufacturers. First, manufacturers provide highly competitive prices because of the region’s low-cost production methods and easy access to raw materials. In addition, many Chinese manufacturers thrive in providing customizable solutions specific to their clients. Lastly, using advanced technology in production, coupled with adherence to international quality standards, means reliable products at relatively low prices. This makes these manufacturers attractive for businesses needing affordable yet high-quality products.
Importing Process and Quality Assurance from Chinese Suppliers
To begin importing from Chinese suppliers, it usually starts with searching for trustworthy manufacturers on platforms like Alibaba, Global Sources, or even niche directories. After establishing communication with potential suppliers, it is essential to convey product details, prices, and any customization prerequisites. Placing sample orders after negotiating terms of trade and ascertaining the supplier’s capability to maintain quality standards is crucial. After sample approval, buyers can arrange bulk production while safeguarding a trade contract for both parties.
Most businesses utilize third-party inspection services to oversee the manufacturing stages of a specific product to maintain quality assurance. These inspections include pre-production, mid-production, and pre-shipment. The quality control process assists in defect detection and monitoring compliance with set standards. Also, certifications like ISO 9001 or other international standards enhance the manufacturers’ reliability. Proper communication, documentation, and frequent inspections smoothen the importing process, making it free of complications and ensuring quality assurance.
Top HDPE Tarpaulin Factories in China and Their Specialties
Xiaoshan Hongyuan Plastic Products Co., Ltd specializes in agriculture, construction, and transportation and offers high-quality, customized solutions and HDPE tarpaulins. These products are durable and crafted to withstand water, UV rays, and harsh environmental conditions.
Shandong Shouguang Longxing Agricultural Film Co., Ltd: This factory produces farming tarpaulins, greenhouse covering, and outdoor storage tarpaulins made from HDPE. They are known for having advanced eco-friendly production facilities that ensure tarp reliability and durability.
Taizhou Tianlu Plastic Co., Ltd: Taizhou Tianlu Plastic Co. Ltd manufactures lightweight but strong HDPE tarpaulins designed for commercial and industrial coverage. With over 15 years of experience, they excel in creating heat-sealed edges and reinforced corners, which provide excellent protection from adverse weather conditions.
These factories produce competitively priced and certified products, which help them establish their reputation in the international market, considering the distinct industry demand and global quality standards.
References
Frequently Asked Questions (FAQ)
Q: What are the different tarpaulin products we manufacture, and what sizes are available?
A: As a leading HDPE tarpaulin manufacturer, we produce a comprehensive range of products, including waterproof tarpaulin sheets, HDPE tarpaulin rolls, PVC tarpaulins, and poly tarps. Our products are available in various sizes, from standard dimensions to custom measurements based on client requirements. All our tarpaulins are made from premium quality woven HDPE or high-density polyethylene fabric, with options ranging from lightweight 200 GSM to heavy-duty variants. We use virgin raw materials to ensure durability and longevity, making our products suitable for multiple applications, from warehouse protection to outdoor coverings.
Q: What are the benefits of working with a top HDPE tarpaulin manufacturer?
A: Working with one of the best manufacturers provides numerous advantages. Our HDPE waterproof tarpaulins offer superior protection against all weather conditions. The multipurpose nature of our products makes them versatile for various applications. We ensure quality control at every production stage, producing consistently durable products. Our manufacturing expertise allows us to create tarpaulins with multiple layers of HDPE for enhanced strength. Additionally, our tarps are easy to handle and lightweight yet robust, and we provide competitive pricing with flexible minimum order quantities. As industry leaders, we offer expert guidance on selecting the right tarp for your needs.
Q: How can I identify the best HDPE tarpaulin for my needs?
A: The best HDPE tarpaulin for your needs depends on several factors. First, consider the intended use – whether you need it for construction, agriculture, or transportation. Look for heavy-duty options with reinforced edges and UV resistance for outdoor applications requiring maximum protection. Check the GSM (grams per square meter) – a higher GSM, like 200 GSM, indicates a thicker, more durable material. Verify that the tarp is made from raw virgin rather than recycled plastics for better longevity. Also, ensure proper HDPE laminated construction with heat-sealed seams for actual waterproof performance. Our experts can help you evaluate these factors to find the perfect tarp for your requirements.
Q: Are your HDPE tarpaulin rolls fully waterproof, and how is this achieved?
A: Yes, our HDPE tarpaulin rolls are 100% waterproof. This is achieved through a specialized manufacturing process, creating multiple layers of HDPE (high-density polyethylene) laminated to form an impermeable barrier. Our waterproof tarpaulin sheets feature heat-sealed seams rather than stitched ones, eliminating potential entry points for moisture. The HDPE polyethylene material is naturally water-resistant; our additional treatments enhance this property. We also incorporate UV stabilizers and anti-fungal agents to prevent degradation from environmental factors that could compromise waterproofing. Our quality control process includes rigorous water resistance testing to ensure every tarp meets our high standards.
Q: What makes your company one of the best heavy-duty tarpaulin suppliers?
A: Our reputation as one of the best heavy-duty tarpaulin suppliers stems from our commitment to quality and innovation. We use only premium woven HDPE fabric in our manufacturing process, ensuring exceptional tear resistance and durability. Our production facility in Ahmedabad utilizes advanced technology to create tarpaulins that exceed industry standards. We offer comprehensive customization options, including size, thickness, and color (companies of all colors are served). Our quality control is rigorous, with each batch tested for tensile strength, water resistance, and UV protection. Our customer service includes expert consultation, prompt delivery, and after-sales support, creating a complete package that distinguishes us from other suppliers.
Q: How do PVC tarpaulins compare to HDPE tarpaulins regarding durability and applications?
A: PVC and HDPE tarpaulins serve different purposes based on their unique properties. PVC tarps typically offer superior resistance to chemicals, oils, and acids, making them ideal for industrial environments. They’re generally heavier than HDPE but provide excellent tear resistance. On the other hand, HDPE tarpaulins are lighter, more flexible, and often more affordable. They provide excellent waterproof protection while being easier to handle and transport. HDPE tarps are particularly suitable for construction sites, agriculture, and transportation. Both materials can be manufactured to be UV-resistant and waterproof. The choice between PVC and HDPE should be based on your specific application requirements, budget considerations, and handling preferences.
Q: Why is Ahmedabad recognized as a hub for quality tarpaulin manufacturing?
A: Ahmedabad has established itself as a premier center for tarpaulin manufacturing due to several key factors. The city benefits from a strategic location with excellent logistics infrastructure, facilitating efficient distribution across India and internationally. Ahmedabad has a rich textile manufacturing heritage has evolved to include technical textiles like tarpaulins. The region has a concentrated ecosystem of raw material suppliers, skilled labor, and specialized machinery manufacturers specific to the tarpaulin industry. Manufacturing units in Ahmedabad, including our facility, have adopted modern technologies while maintaining cost-effective production methods. Additionally, the competitive manufacturing environment has driven continuous innovation in waterproof fabric technology and production processes, establishing Ahmedabad-made tarpaulins as synonymous with quality and reliability.
Q: What quality standards do your tarpaulin rolls meet, and how do you ensure consistency?
A: Our tarpaulin rolls meet and exceed international quality standards, including ISO certifications specific to technical textiles. Each batch undergoes rigorous testing for tensile strength, tear resistance, puncture resistance, and waterproofing capability. We maintain consistency through a controlled manufacturing environment and strict adherence to established production protocols. Our quality assurance process includes regular testing of raw materials – we exclusively use virgin raw materials rather than recycled plastics to ensure uniform quality. We employ advanced machinery calibrated to precise specifications and conduct regular maintenance to prevent variations in output. Every roll is individually inspected before packaging, and we maintain comprehensive quality records for traceability. This systematic approach ensures that RocTarp is recognized as a consistently high-quality HDPE and polyester tarpaulin manufacturer.